

Well trained and experienced operators can spot these quality issues, unfortunately such operators are not always available and the checks to an inexperienced operator then become subjective, not the case with the PATROLMAN™ range of products, all of the subjectivity is eliminated and replaced with quantifiable data. This data is both a time and position dependent so if for any reason the product passes through the induction machine at a different SPEED, the transferred energy will be altered and the induction sealing result will be different. To an operator a 10% change in the speed of a product conveyor may not be noticed. Just a 1mm HEIGHT adjustment of the sealing head may have occurred, or a 5 degree ANGLE change in guide rails may be missed. The induction sealing setting on the induction sealing machine will not have changed at all, yet the sealing results would have negatively changed significantly!
The PATROLMAN™ range of quantifiable validation systems provides a visual and measured count of the energy that is transferred between the induction equipment and the induction seal, this validation occurs when the a Master Sensor is passed along the same path as the products during a production run. What might look like an identical set-up from the last time an induction machine was run, the PATROLMAN™ range ensures all of the parameters are optimized?
The PATROLMAN™ range has dedicated equipment that meets the requirements of the different filling lines, whether you need the LINEMASTER™ a flexible system for a variety of bottle shapes and sizes operating at lower speeds, or the SEALMASTER™ a dedicated system for high speed lines that have minimal variation in the size of the container and closure. Finally there is the HANDMASTER™ that meets the needs of manual hand induction lines, the same great technology that allows a quality assurance process and monitoring on your hand induction sealing line.
The PATROLMAN™ range takes away the guess work on the amount of energy that is being transferred and provides the operator with confidence that the filling line is set to the optimized settings, giving the brand owner peace of mind and the consumer a perfect package every time.
-
Overheating – there are a number of factors to show if there has been overheating including – visual dis-colouration of one or more layers of the induction foil, bubbling or creasing, a flattening of the bottle neck, melting of a backing resealing foam (when present).
-
Uneven heat sealing –The foil can look well sealed but an uneven heat seal can result in areas of the seal being too firmly “welded” or very lightly welded making the seal likely to fail with a little pressure on the side walls of the bottle/container.
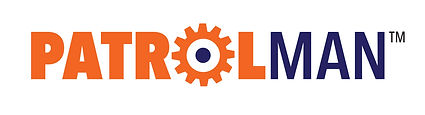
Because there are various unseen factors that can significantly affect the sealing performance of an induction Liner it is always recommended to have an induction sealing - quantifiable validation QA system. There is always the risk that the sealing machine may be knocked out of line, height adjustment might have been made, blown bottle height variations, and conveyor speed alterations can all significantly impact negatively on the induction sealing results.
Some things to look for include:
-
Correct Settings – An experienced operator would know to look for a concentric heat pattern in the foil; by holding the foil to a light source at the correct angle he would see a smaller circle where material has not been affected by heat. This means the seal has heated from the outside inwards in an even pattern; hence an even seal.
Follow us